3D printing technology has opened up new possibilities for the production of complex components in the aerospace industry. The use of printed ducting in aircraft and aerospace products has enabled the production of lightweight and high-strength components that get to market faster and improve fleet readiness.
Manufacturing Solutions for Aircraft Ductwork
The Different Types of Aviation Ducting
Ducting is a component used in aircraft and aerospace products to channel air or fluids from one place to another. It can be found in the engine, environmental control system, or avionics cooling system. Ducting can be made of various materials, such as aluminum, titanium, or composite materials. The design of the ducting is critical for the efficient operation of the aircraft or aerospace product.
This type of ducting is used to transport air throughout the cabin for heating, ventilation, and air conditioning purposes. ECS ducting is typically made from aluminum or titanium and is designed to withstand high pressures and temperatures. Additive manufacturing is used to produce ECS ducting components to optimize airflow.
Engine ducting is used to transport air to and from the aircraft’s engines for cooling, while fuel ducting moves fuel through the aircraft. Engine ducting is typically made from aluminum or titanium and is designed to withstand high temperatures and pressures. 3D printed polymer-based and metal-based materials can be utilized, which improve performance and cost savings.
This type of ducting is used to transport air to cool the aircraft’s avionics systems, which include the electronic systems that control the aircraft’s flight and navigation. Avionics cooling system ducting is typically made from metal and is designed to withstand high temperatures and pressures.

Use Case for Metal Versus Polymer Components
Aircraft ductwork that carries high-pressure air or exhaust gases is made from metal, while lower-pressure ductwork may be made from polymer materials. In commercial aircraft, the majority of air ducting is made from metal, typically aluminum or titanium, due to their high strength and ability to withstand high temperatures and pressures. The ducting in the engine and avionics cooling systems is also made from metal to withstand the engine environment.
Polymer ducting may be used for low-pressure applications, like in smaller general aviation aircraft and some military aircraft. Polymer ducting is lighter than metal and can be more easily molded into complex shapes, making it useful in situations where weight and space are at a premium.
How is Ducting Produced in the Aerospace Industry?
3D printing technology has enabled the production of complex shapes and structures that were previously impossible to manufacture using traditional manufacturing methods. The use of 3D printing technology in the aerospace industry has enabled the production of lightweight and high-strength components, including ducting.
There are various 3D printing technologies used in the production of ducting, such as Fused Deposition Modeling (FDM), Stereolithography (SLA), Selective Laser Sintering (SLS), and Direct Metal Laser Sintering (DMLS). Each technology has its strengths and weaknesses and is used depending on the requirements of the application.
Fused Deposition Modeling (FDM)
FDM is one of the most commonly used 3D printing technologies for the production of ducting in aircraft and aerospace products. It is a cost-effective and efficient method for producing low-volume parts with complex geometries. FDM technology uses a thermoplastic material that is extruded through a nozzle and deposited layer by layer to create the final part.
FDM technology has its limitations in terms of strength and porosity. However, recent advances in FDM technology have addressed these limitations. Companies like ADDMAN have developed software plug-ins that can reduce porosity and increase part strength by up to 75%.
Stereolithography (SLA)
SLA is a 3D printing technology that uses a laser to cure liquid resin into solid parts. SLA is commonly used in the aerospace industry for its ability to produce parts with high accuracy and excellent surface finish. In aircraft ducting production, SLA is used to create ducting prototypes and small production runs. By using SLA, manufacturers can quickly produce high-quality, functional prototypes and small production runs of aircraft ducting for testing and validation purposes.
Direct Metal Laser Sintering (DMLS)
DMLS is a 3D printing technology that uses a laser to fuse metal powder into solid parts. DMLS is commonly used in the aerospace industry for its ability to produce high-strength and lightweight parts. In aircraft ducting production, DMLS is used to create metal ducting that can withstand high temperatures, pressures, and chemical exposure. By using DMLS, manufacturers can create aircraft ducting with complex shapes and internal geometries that cannot be achieved with traditional manufacturing methods. DMLS is commonly used in the production of avionics cooling system ducting in military aircraft, where high performance and durability are essential.
Implications of Reducing Porosity
Porosity in airplane duct components is a critical issue, as even small leaks can negatively impact performance and safety. For aerospace applications, reducing porosity in duct components is essential to ensure their reliability and safety. Additionally, reduced porosity can improve the strength and durability of the duct components, leading to longer service life and reduced maintenance costs. Through advanced additive manufacturing techniques, ADDMAN has been able to significantly reduce porosity for Fused Deposition Modeling (FDM) parts for customers, resulting in parts that are 100x less porous and stronger, all the while more affordable.
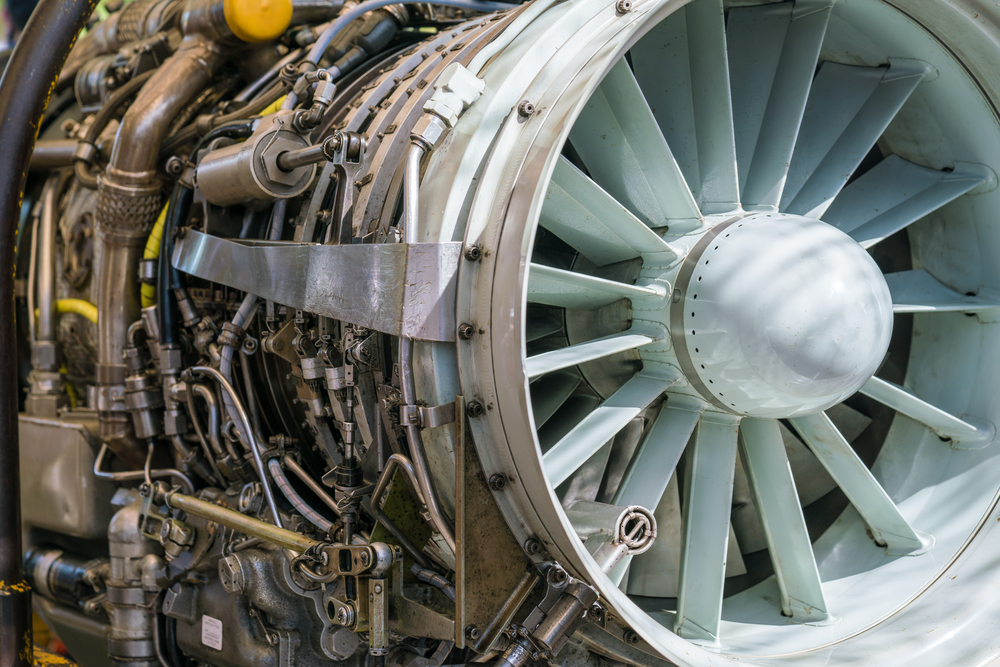
FDM Delivers Low Cost Ductwork
With the help of ADDMAN’s proprietary ADDCAAM software and methodology, a customer was able to produce air intake duct parts with Fused Deposition Modeling (FDM) technology at a 15% lower cost than the customer’s legacy Multi Jet Fusion (MJF) production methods. In addition to the cost savings, the FDM parts were also 70% stronger and 100x less porous, resulting in improved performance and durability. This success demonstrates the effectiveness of ADDMAN’s advanced technology and its ability to deliver superior results for aerospace applications.
Additive manufacturing is the ideal solution for producing complex, lightweight, and high-strength ductwork that meets the demands of modern aircraft.
Materials Used to 3D Print Ductwork
The choice of material for 3D printed ducting depends on the application requirements, such as strength, temperature resistance, and weight. Some of the commonly used materials for 3D printed ducting are:
Polycarbonate (PC) – Polycarbonate is a popular material for 3D printed ducting due to its high strength and temperature resistance. It is also lightweight, making it an ideal material for aircraft and aerospace applications. Polycarbonate is commonly used for ducting in small aircraft, such as single-engine planes, as well as for environmental control system ducting in commercial airliners. It is also used for avionics cooling system ducting in military aircraft.
Ultem – Ultem is a high-performance thermoplastic that is commonly used in the aerospace industry for its high strength, temperature resistance, and chemical resistance. It is an ideal material for ducting in high-performance military aircraft and commercial airliners. Ultem is commonly used for environmental control system ducting, as well as for avionics cooling system ducting in military aircraft.
Nylon – Nylon is a strong and flexible material that is commonly used for ducting in aircraft and aerospace products. It has excellent mechanical properties and can withstand high temperatures. Nylon is commonly used for ducting in small aircraft, such as single-engine planes, as well as for environmental control system ducting in commercial airliners. It is also used for avionics cooling system ducting in military aircraft.
Carbon Fiber – Carbon fiber reinforced materials are commonly used in 3D printed ducting for their high strength and stiffness. They are also lightweight, making them ideal for aerospace applications. Carbon fiber reinforced materials are commonly used for avionics cooling system ducting in high-performance military aircraft, such as fighter jets.
Stainless Steel – Stainless steel is a popular choice for ductwork in both the environmental control system and the engine systems of an aircraft. It is strong, corrosion-resistant, and able to withstand high temperatures and pressures.
Inconel – Inconel is a high-performance alloy that is commonly used in aircraft engine ducting due to its high temperature resistance and ability to withstand thermal fatigue. It is also corrosion-resistant and has good mechanical properties at high temperatures.
Titanium – Titanium is a lightweight and corrosion-resistant metal that is commonly used in both ECS and engine ducting. It is strong, ductile, and able to withstand high temperatures and pressures.
Aluminum – Aluminum is a widely used material in aircraft ducting due to its light weight, good strength-to-weight ratio, and high corrosion resistance. It is commonly used in ECS ducting, avionics cooling system ducting, and fuel ducting.
In addition to the specific types of aircraft and aerospace products mentioned above, the choice of material for 3D printed ducting also depends on the specific application requirements. For example, the type of material used for ducting in an engine will be different from the type of material used for environmental control system ducting or avionics cooling system ducting. The operating conditions of the aircraft or aerospace product, such as temperature and pressure, also play a role in the choice of material.
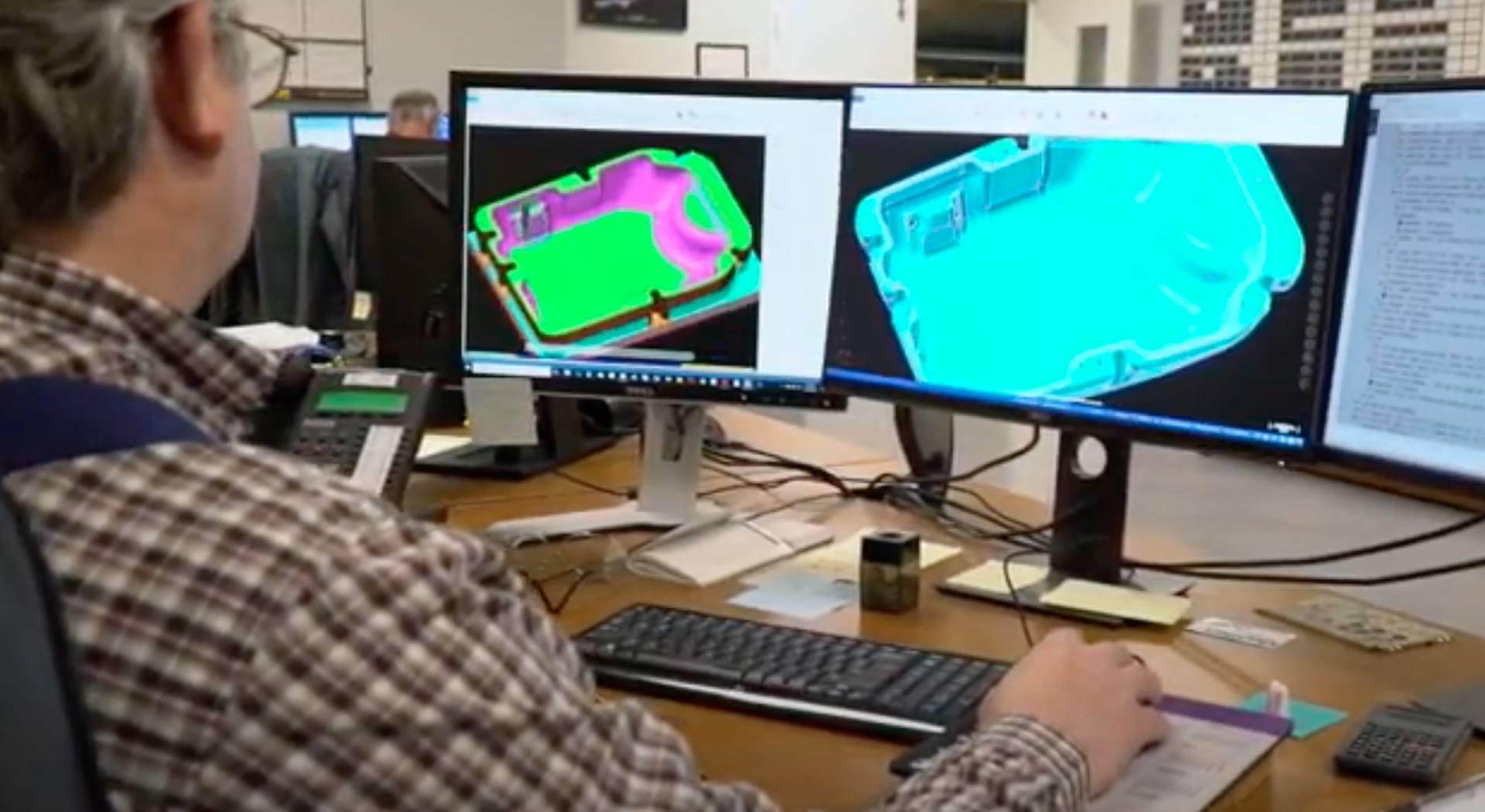
Innovation to Increase Component Strength
Additively manufactured aircraft ducting can now benefit from InterFill 3D, a powerful software tool powered by ADDMAN and our innovative Computer Aided Additive Manufacturing (CAAM) methodology. This printer-agnostic build prep tool offers industry-leading part strength by converting conventionally sliced files into an interlocking infill structure, resulting in parts that are 70% stronger and have 100x less porosity. With InterFill 3D, additively manufactured aircraft ducting can now achieve unparalleled strength and durability, making it an ideal solution for the most demanding aerospace applications.
Weighing the Benefits of Traditional and Additive Manufacturing
Traditional manufacturing methods may make more sense for ductwork in certain situations. ADDMAN is proud to provide additive manufacturing, injection molding, and CNC machining services to meet the demands for our customers parts no matter the volume or product lifecycle stage.
High-Volume Production – If a large number of identical ductwork parts need to be produced, traditional manufacturing methods like injection molding may be more cost-effective and efficient than additive manufacturing.
Large-Scale Ducting – For very large ducting components, traditional manufacturing methods like welding or rolling may be more practical and cost-effective than additive manufacturing, which may be limited by the size of the build envelope of the 3D printer.
Specialized Materials – Traditional manufacturing methods may be better suited for ducting that requires specialized materials that are not compatible with additive manufacturing, such as certain high-temperature alloys or composite materials. ADDMAN routinely breaks barriers for what is possible with AM, and we encourage a materials and process consultation for your parts.
Regulatory Compliance – In some cases, traditional manufacturing methods may be preferred over additive manufacturing due to existing regulations or certification requirements that require the use of specific manufacturing methods or materials.