ADDCAAM™ optimizes FDM printing with advanced slicing technology, producing stronger, more durable parts with dramatically reduced porosity—without changing your printer or materials.
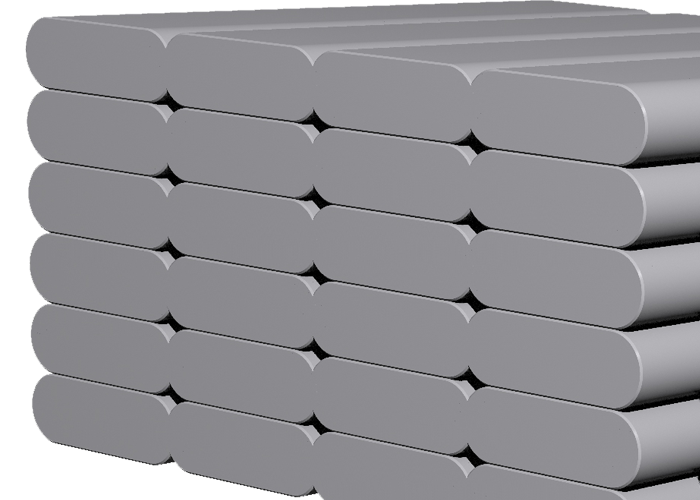
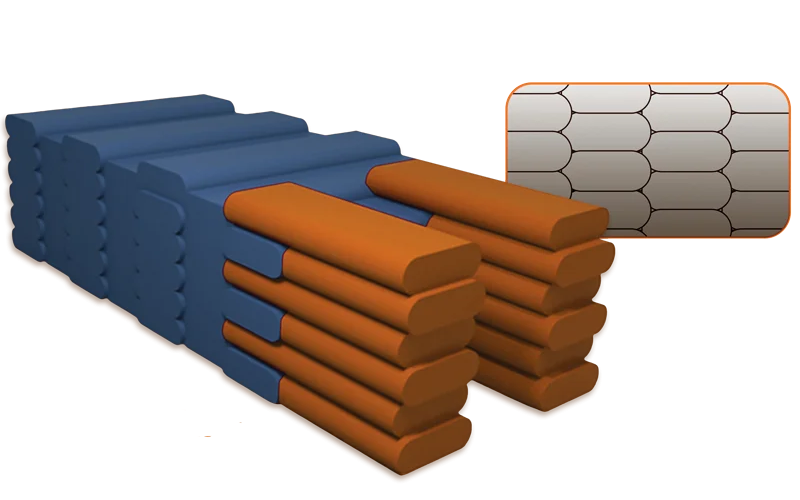

Discover all the benefits
Now available as a Real Vision Pro plugin, ADDCAAM delivers next-level slicing performance without requiring additional hardware or complex setup, making industrial-strength FDM printing easier to adopt than ever before.
Enhances layer adhesion with InterLace technology, creating prints that are up to 70% stronger than traditional FDM.
InterLocking InFill eliminates continuous stress paths, reducing porosity by 100x for more durable, airtight, and watertight parts.
Advanced toolpath optimization strengthens parts without increasing print speed, ensuring efficiency in production.
Interwoven infill structures provide better stress distribution, minimizing weak points and delamination risks
ADDCAAM optimizes FDM printing to meet the rigorous demands of aerospace, automotive, and defense industries. By reinforcing layer bonds and reducing porosity, it enables lightweight, high-strength polymer components that can withstand extreme conditions—expanding the viability of FDM for mission-critical applications.
