Welcome to our comprehensive guide on Additive Manufacturing (AM), a revolutionary technology that is transforming the way we design, create, and produce objects. From intricate jewelry pieces to high-performance aerospace components, AM offers unparalleled flexibility and efficiency in manufacturing operations. In this guide, we’ll walk you through the step-by-step processes of two major AM categories: Metal and Polymer Technologies.
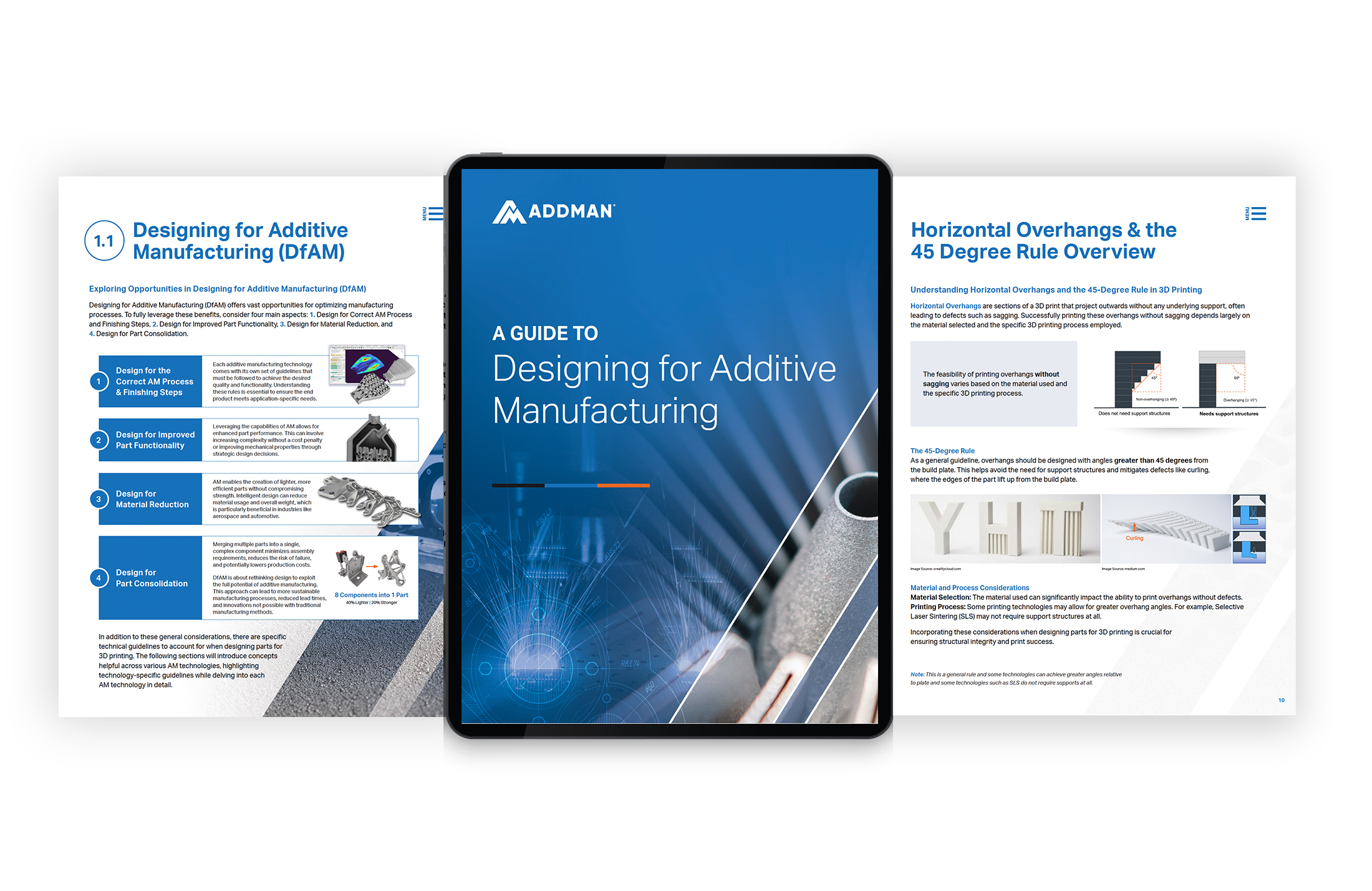
Metal AM
- Complex Geometries: AM enables the creation of intricate and complex geometries that were once impossible with traditional manufacturing methods. This opens up new design possibilities, especially in industries like aerospace and automotive, where lightweight and intricate components are essential.
- Reduced Material Waste: Traditional subtractive manufacturing methods often involve removing excess material from a larger block, resulting in substantial waste. With AM, material is deposited only where needed, minimizing waste and optimizing material usage.
- Rapid Prototyping: Metal AM allows for quick and cost-effective prototyping of parts and components. This is invaluable for testing and refining designs before committing to full-scale production.
- Customization: AM makes it possible to create highly customized and tailored metal parts for specific applications, catering to individual requirements and reducing the need for extensive tooling changes.
- Reduced Lead Times: The elimination of tooling and molds in the AM process significantly reduces lead times, enabling faster product development cycles and quicker time-to-market.
Polymer 3D Printing
- Precision and Detail: Polymer AM technologies like DLP and SLA excel in producing high levels of precision and intricate detail, making them ideal for industries such as jewelry and dentistry, where fine details matter.
- Customization: Just like in metal AM, polymer AM offers the ability to create customized products tailored to individual needs, ranging from dental implants to personalized consumer goods.
- Diverse Material Properties: Different polymer materials can be used in AM, each with its own set of mechanical, thermal, and aesthetic properties. This versatility allows for the production of a wide range of end-use products.
- Reduced Assembly: AM can produce complex parts as a single unit, eliminating the need for assembly of multiple components. This not only simplifies production but also enhances the final product’s structural integrity.
- Functional Prototyping: Polymer AM allows for the creation of functional prototypes that closely mimic the properties of the final product, facilitating more accurate testing and validation.
- Low Volume Production: For small-scale production runs, polymer AM offers a cost-effective alternative to traditional molding processes, as it doesn’t require expensive molds or tooling.
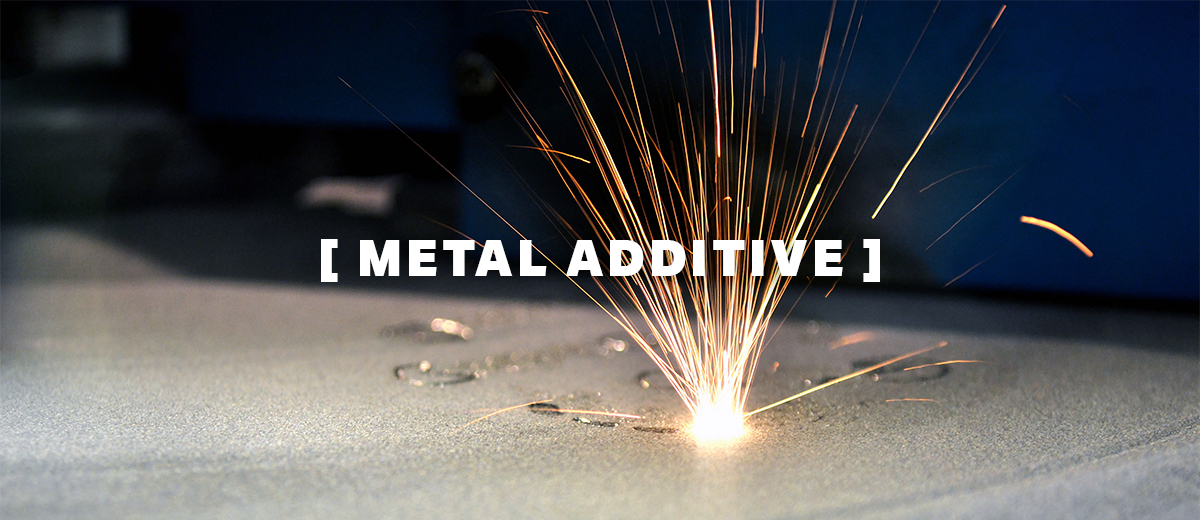
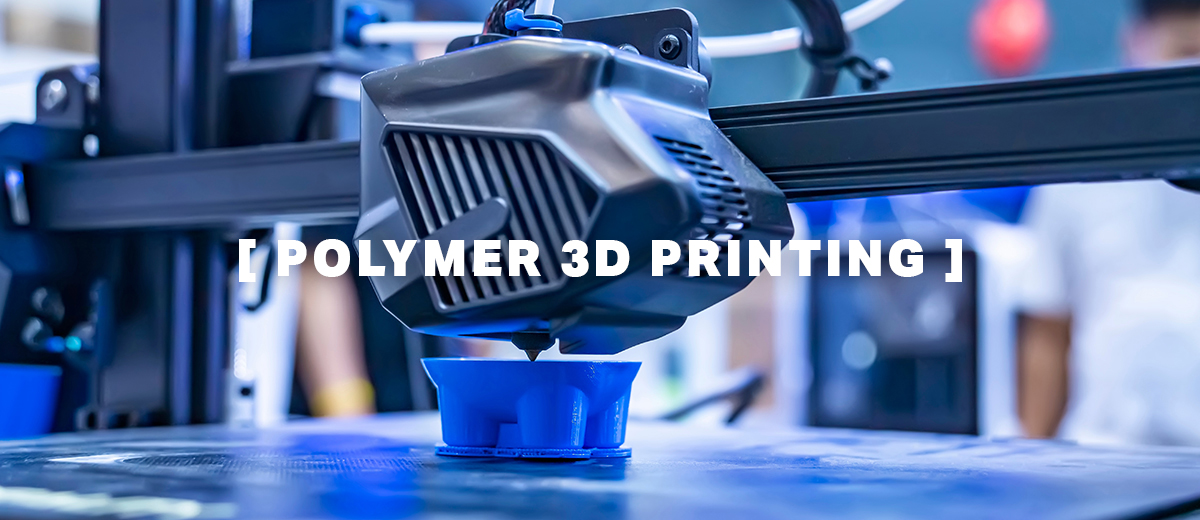
Digital Light Processing (DLP)
- Design the object using CAD software, ensuring it’s tailored for AM’s capabilities.
- The CAD model is sliced into layers, guiding the printing process.
- A projector exposes a liquid photopolymer resin to light, solidifying the resin layer by layer to create the object.
- Post-processing involves removing excess resin, and curing the object under UV light to strengthen its mechanical properties.
Digital Light Synthesis (DLS)
Combining light and oxygen, DLS creates detailed objects from liquid photopolymer resin, offering smooth surfaces and strong mechanical properties.
- Design the object using CAD software.
- The CAD model is sliced, and liquid resin is spread across a platform.
- Oxygen is selectively introduced to prevent certain areas from curing.
- A combination of light and oxygen solidifies the resin layer by layer, forming the final object.
- Post-processing includes cleaning, curing, and potentially additional treatments for mechanical strength.
Fused Deposition Modeling (FDM)
- Design the object and slice the model into layers.
- Thermoplastic filament is melted and deposited layer by layer onto the build platform.
- The object gradually takes shape as each layer fuses with the previous one.
- Post-processing may involve removing support structures and using surface finishing techniques for enhanced appearance.
Fused Filament Fabrication (FFF)
- Design the object and slice the model into layers.
- Thermoplastic filament is melted and deposited layer by layer onto the build platform.
- The object gradually takes shape as each layer fuses with the previous one.
- Post-processing may involve removing support structures and using surface finishing techniques for enhanced appearance.
Hybrid PhotoSynthesis (HPS)
This innovative technology combines DLP and laser light for speed and quality.
- Design and slice the model.
- Liquid photopolymer resin is exposed to DLP and laser light simultaneously, solidifying the resin rapidly.
- Post-processing steps are similar to those of DLP.
Multi Jet Fusion (MJF)
- Design, slice, and spread powdered material.
- An inkjet array selectively deposits binding agents and detailing agents onto the powder.
- Thermal energy is applied to fuse the powdered material, layer by layer.
- Post-processing includes removing excess powder and potentially applying color.
Polyjet
- Design and slice the object.
- Liquid resin is jetted onto the build platform and cured instantly using UV light.
- The process repeats, layer by layer, with the ability to create multi-color and multi-material prints.
- Post-processing may involve support removal and additional finishing for smoother surfaces.
Selective Laser Sintering (SLS)
- Design, slice, and spread powdered material.
- A laser selectively sinters the powder, fusing it layer by layer.
- The object forms as unsintered powder supports it during the printing process.
- Post-processing includes removing excess powder and potentially heat treatment for improved strength.
Stereolithography (SLA)
- Design and slice the model.
- A laser or light source selectively cures liquid resin, layer by layer.
- The object is built within a liquid resin bath.
- Post-processing involves cleaning, curing, and potential finishing steps.